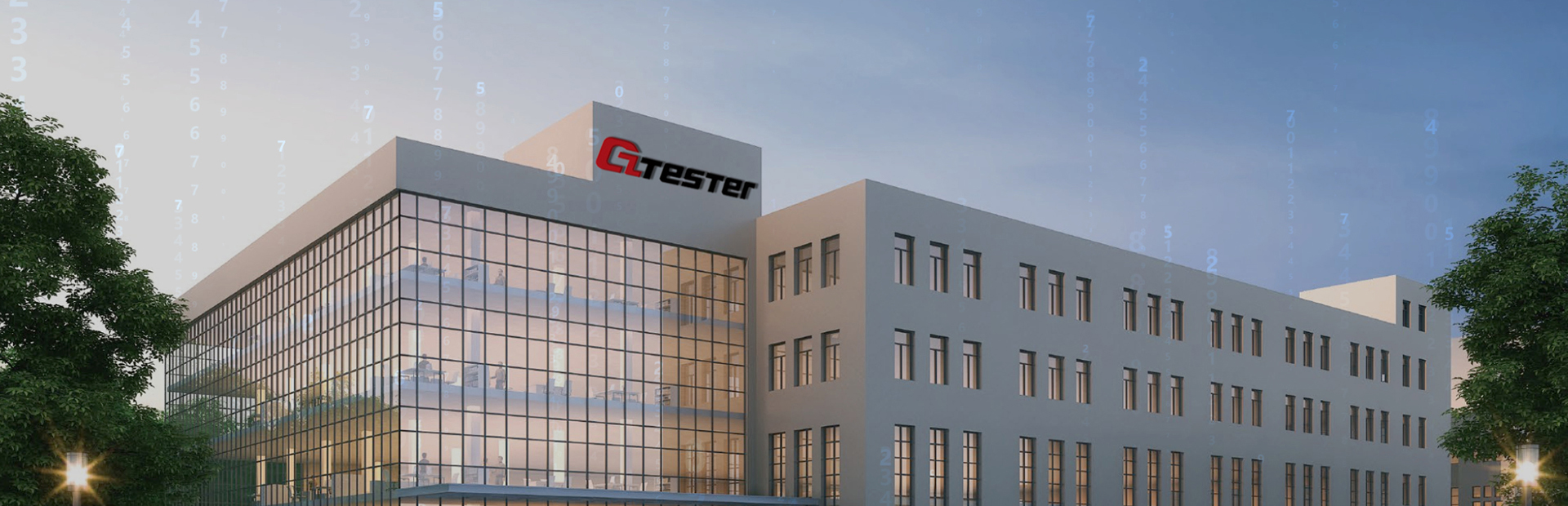
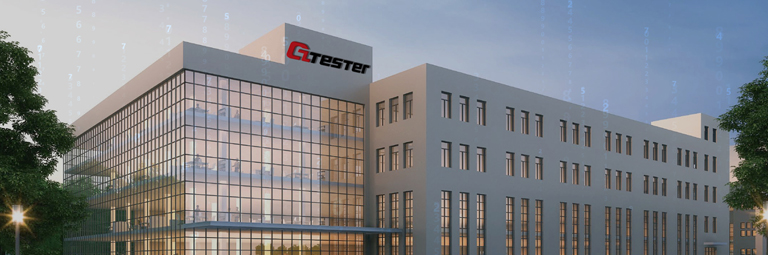

Intelligent Networking
Escort for safe driving
Customer-centric,market-oriented,innovation-oriented, em-ployee-oriented, empowering automotive electronics, new energy, and escort for safe driving
-
Perception
Radar
-
Decision Making
DCU
-
ActuationEHBEPS
-
Communication
T-Box
-
Intelligent Networking
-
-
- Process flow: Manual loading station ->Tunnel heating furnace ->Docking station->High temperature testing station ->Cooling station ->Normal temperature testingstation ->Manual unloading station. By connecting all testing stations in seriesthrough the up and down circulating conveyor lines, for product heating (≤ 80 ℃), theconveyor tray directly enters the double speed chain heating tunnel furnace
- Product traceability: The device is equipped with a barcode scanner to identify the QRcode on the components or products.
- Provide production line level MES to achieve data exchange, traceability, reporting, and production process management (including defective product management) of theproduction line.
-
-
- Unmanned operating system
It can be equipped with automatic plate loading machine, In Line ICT / FCT is equipped with automatic code scanning function, automatic pressure testing; - Quality identification system
Functoon Buffer loaders separate the products into good and defective ones, and the good ones are tested in double-layer FCT.Equipped with un-loader ON[OK] to separate and collect good and defective products, PCBA can be fully automated - Multiple system test modules
In Line ICT double-layer FCT equipment is equipped with elevator itself. Two sets of test systems work simultaneously,which can provide twice the efficiency
-
-
- DIP inserts, welding, testing, dispensing/three-proof, split plate,automatic unloading, automatic sorting of good and bad products;
- Fully automatic lnline design, no manual operation, test speed 30% faster than manual, unmanned operation;
- Support product traceability,rapid line change, through the combination of man and machine, with the help of vehicles to achieve personnel reduction, to improve production efficiency and product quality
-
-
- Suitable for general PCBA product test with process
-
- It is suitable for PCBA FCT and EOL test.
-